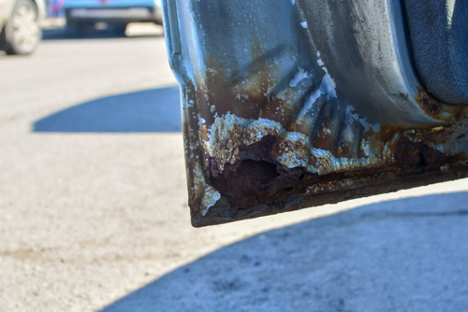
The condition of a material is bound to deteriorate with time no matter how tough its mechanical properties are. Natural elements and the conditions to which it is subjected to play a big role in this.
For example, water facilitates rusting of iron materials thus making them weak and susceptible to a variety of destructive forces. Thus it is important that the materials be protected from such entities to preserve their effectiveness and durability.
This is especially true for mission-critical parts that have a huge impact on the operation of the whole system. Here are some of the things that you should know about wear-resistant coating and more.
What is wear-resistant coating?
It refers to a general form of protection given to materials by covering them with a layer that shields them from the entities that cause deterioration.
There is a variety of techniques used to implement this but they all work to achieve the same results. Suitability depends on the task at hand and the conditions involved.
As such, one must be aware of the mechanisms or elements that the equipment is susceptible to for them to be able to identify the appropriate technique to use. Here are some of the most common methods and the applications that they are suited for.
- Nitriding
As the name indicates, it involves the use of nitrogen. The covering layer contains nitrogen which is infused through thermochemical process hence resulting in a hard protective coat. A good application area is the protection of titanium against abrasion. The treatment process is done under high temperatures hence might not be suitable for some materials.
- Hard anodization
It entails the use of heat to produce an oxide that forms a strong coating. The smooth resultant surface minimizes friction hence this is a great technique to use on moving parts. It can be used on a light metal such as aluminum. The downside is that it doesn’t support applications that are characterized with heavy loads due to the structure of the covering layer. It contains micro-cracks that can concentrate stress.
- Plasma Electrolytic Oxidation
This involves the use of an electrolyte and electrical energy to produce plasma and oxide that integrates to form the protective cover over the metal.
It is one of the most effective methods in use. The layer produced is as a result of both chemical and physical alterations that makes the final product resistant to both mechanical wear and corrosive elements.
It also has good environmental friendliness ratings. The disadvantage is that the resulting surface is characterized with coarseness hence finishing procedures are required.
- Electroless nickel
A composite containing nickel as the main element is exposed to a chemical bath to yield the coat. The layer is not only hard but it is also sleek and has a high level of ductility thus preventing wear on gliding parts. Its major shortcoming is that if it is not applied properly or contains defects then it will facilitate corrosion.
What are the factors to consider when choosing?
As mentioned before, the techniques vary in terms of resulting properties hence are suited for different use. Here is what you should take into account. See more here https://www.designworldonline.com/make-right-choice-metal-coating-right-application/
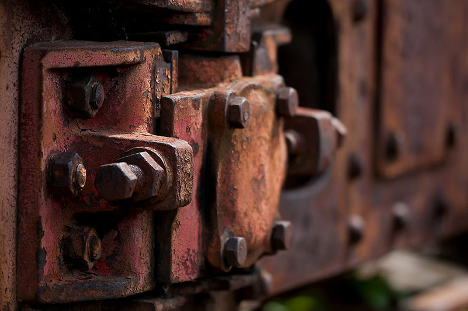
- Maintenance
It should not cause hindrance as far as maintenance of the equipment goes. If anything, it should make the process easier. For instance, those that produce smooth surfaces makes it easy to clean. This helps keep the component in good shape thus increasing the lifetime.
- Performance
If it interferes with the performance of the component then it is not worth it. The coating is supposed to protect and enhance its capabilities to make it more effective. You should opt for a technology that ensures proper integration and flexibility to promote productivity.
- Cost
Choose a cost-effective technique that will ensure that you benefit in the long-run. Don’t just opt for a method just because it is cheap even if it doesn’t properly suit the application. This will backfire and result in a huge loss.
- Compliance
You should consider the regulations that govern the use of coating-methods. Violating them in any way will get you in trouble with the authorities and can also be hazardous to human health and other lives in the ecosystem. Click here to read more insights.
Conclusion
Wear-resistant coating is a descriptive term referring to the use of an external layer of protection or surface to shield a material from entities that would otherwise cause it to wear down. There are several different methods through which it can be implemented. The choice is influenced by the type of application that the material is to be put to. When choosing it is also important to consider other factors such as how it will affect the maintenance, performance, cost, and regulations. Make sure that the technique you choose will best suit the task at hand.