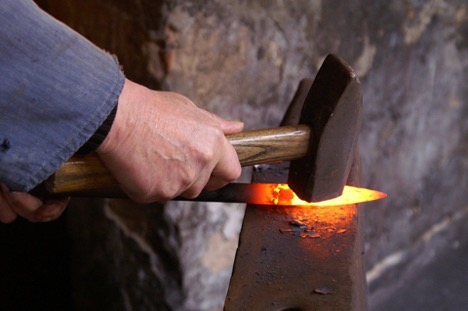
Forging is the procedure of shaping and forming metals using processes like rolling, pressing, and hammering. The entire process will usually start with a cast ingot or a cogged billet with materials like titanium.
The cogged billet will then be heated into a temperature that’s considered its “plastic deformation,” and it’s kneaded between dies to form their desired shapes and size. You may want to check out the process of titanium forge that’s used in many industries. The applications can involve companies that are into submarines, ships, pressure vessels, rockets, helicopters, heat exchangers, and aircraft.
The Process of Forging
Buyers should choose processes from a supplier for the production of the metal component. When it comes to materials and metals, many people are faced with lots of choices and alternatives. Many companies are offering metalworking processes that have their own advantages, specific costs, and capabilities as well.
The forging process is well-suited when it comes to making parts, like helicopters, automobiles, or gearboxes. However, some may not be aware of these advantages, and they may need further research, especially if they are not familiar with the forging industry.
The process can provide optimum quality to parts, costs, and durability. The custom parts with suitable sizes are critical when it comes to their performance. For instance, a single part used in helicopters should be precise and strong to withstand wind and pressure in the air.
Several of the processes may include cold forging, closed die, and extrusions. There are pros and cons to be considered, but many may want to get the seamless rolled rings and the open die because of their known benefits. You can know more about die forging on this page here. Meanwhile, here is formation that you may want to know about the production of the metal parts.
The industries were changing, and to meet their massive needs for parts, the forging industry had evolved with several advances. In the past decades, many companies had incorporated robotics, electronic controls, computers, and sophisticated equipment to meet many demands.
Some of the tools proved to be beneficial because they complement human skills well, and they are essential for the success of many companies. The modern forging plants are superior to their older counterparts, and the parts can be produced in various shapes, sizes, finishes, and materials.
About Open Die Forging
The open die process tends to break up the cast’s coast structure and replace them with finer ones afterward. The gas porosity and shrinkage usually found in cast metal are consolidated together through a reduction process that the ingots undergo. Since there’s the growth of new and refined grains that stick together, the overall structural integrity of metals like aluminum becomes robust.
Therefore, a metal’s mechanical property is improved through the reduction, segregation, and making voids on the overall cost structure. The forging process may also mean aligning the grain flow so that the strength direction will be more uniformed.
The secondary treatments like processing in heat can further refine the grains. You can read more about grain refinement in this link: https://www.researchgate.net/publication/257447392_Grain_Refinement_in_a_Low_Carbon_Steel_Through_Multidirectional_Forging. You can choose from myriad shapes and sizes with enhanced properties in forgings, and they are ideal for material manufacturing compared to assemblies or casting.
Information to Know on Forged Titanium
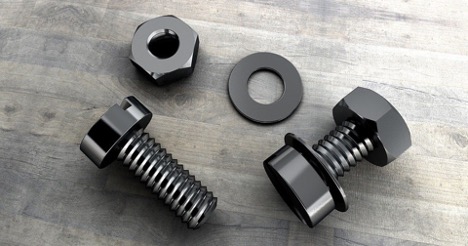
Using titanium as a material is often common in heavyweight industries. This is because this metal provides excellent weight ratios and strength coupled with corrosion resistance. Over 90% of mined titanium is used in the manufacturing process of titanium dioxide, which is a pigment used in cosmetics, plastics, and paints. Only about 5% are refined into its metal form.
Titanium is still a record holder when it comes to density ratio and the highest strength. It provides resistance to corrosion and excellent durability that is not present in other metals. Because of its advantages, it’s often used in saltwater, off-shore, and marine environments. It’s also well-suited in the industry of defense and aerospace because it can withstand intense conditions.
Choosing the Right Company
If you’re a business owner, you may need forging for more durable parts of automobiles. Choosing the right company means that they can provide you with the prototype of the part that you need in no time and they can deliver them faster. For customers who are new in this industry, finding a trusted supplier that can meet all of their specifications can be a challenge.
It’s essential to research the company that you ideally want to manufacture the forged parts, and they should have a track record of delivering high-quality materials. Some can offer engineering guidance, destructive testing, metallurgical review, and finished machine options. You may want to know about other products, including bars, complex shapes, rotor shafts, and different unique geometries that you may need in your company.